La aproape 600 de ani de când Gutenberg inventa tiparnița sa cu litere mobile, nemții s-au pus din nou pe treabă.
Doar că de data asta nu mai tipăresc pe hârtie, ci direct în metal și plastic.
De fapt, din metal și din plastic.
Ca o aripă de pescăruș: cum își poate lua zborul o economie bazată pe printarea tridimensională
Viitorul
30/11/2022
Nu sunt singurii. La nivel global, industria producției aditive - așa cum se numește, de fapt, procesul printării tridimensionale, a adus venituri de peste 10 miliarde de euro în 2021. Până în 2030, va ajunge la 50 de miliarde de euro, conform unei estimări citate de Bloomberg. O creștere extrem de rapidă, cu impact direct într-o mulțime de industrii, în special cea auto.
De ce ar trebui să ne intereseze, de fapt, acest nou procedeu de a fabrica lucruri? Pentru că, fără el, o bună parte din industrie - în special cea de transporturi - ar avea de suferit puternic de pe urma electrificării și a normelor de siguranță tot mai drastice.
Pare o legătură ciudată, însă în realitate de reușita producției aditive depinde în bună măsură atât reușita electrificării mașinilor, cât și dezvoltarea cât mai rapidă a economiei circulare - cea despre care am vorbit mai pe larg într-un articol precedent.
Legătura dintre aripa de pescăruș și mașina ta
Atunci când ai ocazia să ții o pasăre în mâini, rămâi uimit de cât este de ușoară. O mare parte din secretul zborului stă în oasele păsărilor - care sunt mult mai ușoare decât cele ale mamiferelor, de pildă. Forma, densitatea și structura oaselor au fost selectate prin procese evolutive pentru a le permite păsărilor să-și dezvolte aripi cu care să zboare cu un consum de energie cât mai mic.
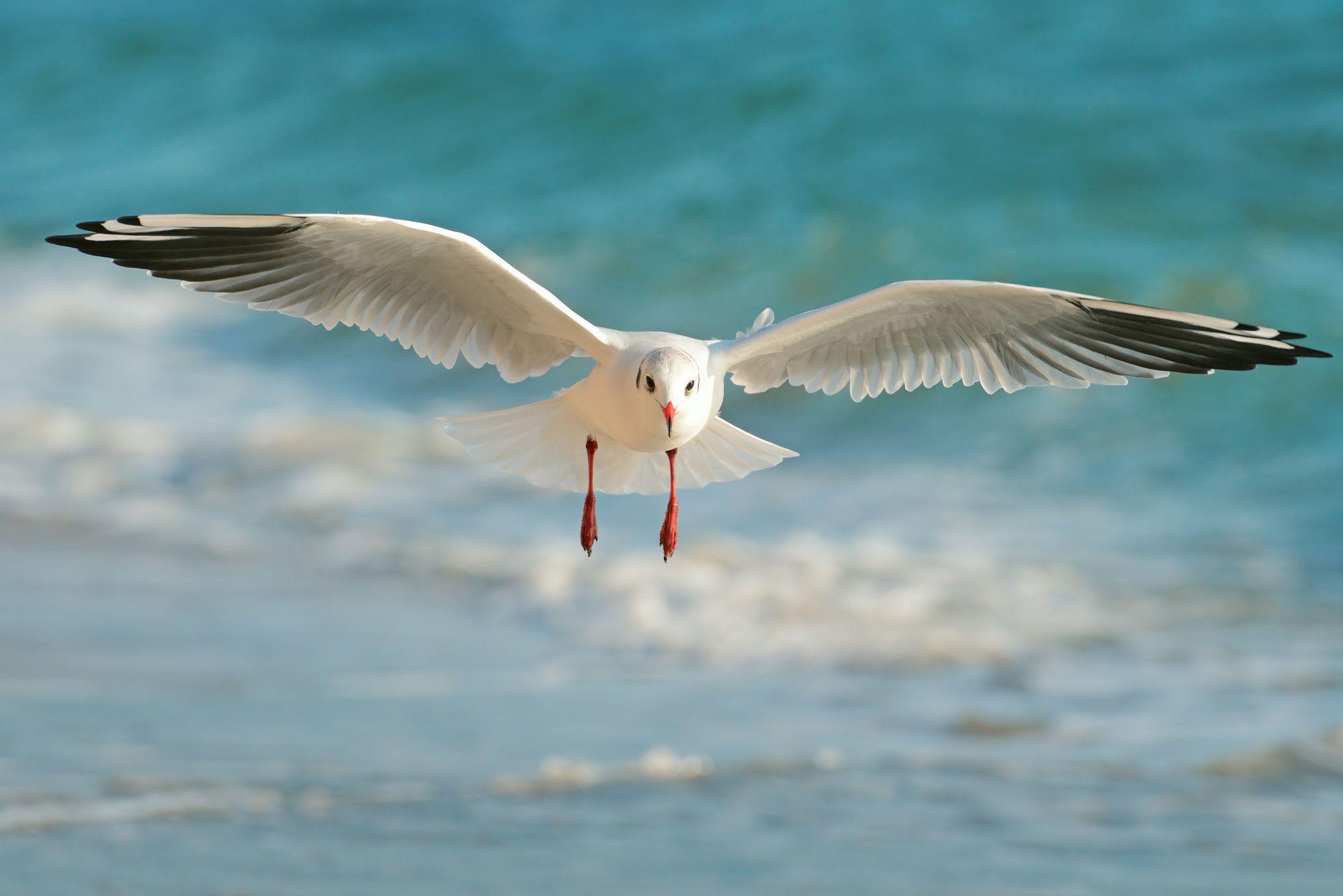
Ușor, rapid, economic - perfect adaptat să-ți fure mâncarea. Foto: © Alinamd | Dreamstime.com
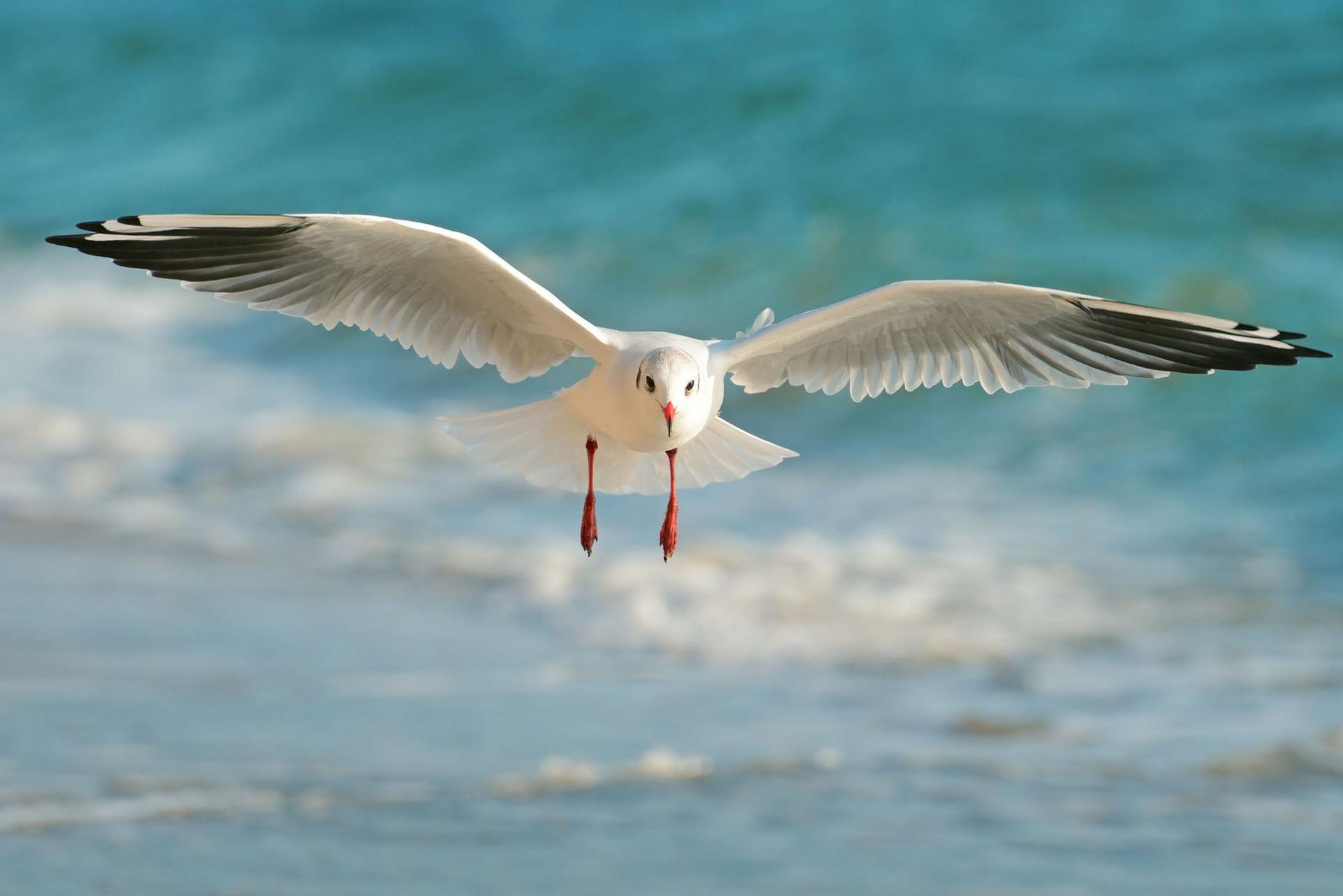
Ușor, rapid, economic - perfect adaptat să-ți fure mâncarea. Foto: © Alinamd | Dreamstime.com
Ei bine, când te uiți la mașina ta, oricare ar fi ea, a fost selectată prin procese industriale ca să devină cât mai economică, cât mai sigură, confortabilă și (eventual) cât mai rapidă. Patru direcții esențiale care se bat cap în cap, pentru că spre deosebire de păsări, noi le vrem pe toate deodată.
Din 1981 până acum, greutatea mașinilor a crescut în medie cu 30%. Asta înseamnă peste 300 de kilograme în plus la o mașină de familie obișnuită, indiferent de marcă sau segment!
Mare parte din creșterea în greutate e cauzată tocmai de standardele tot mai înalte de siguranță și confort, iar doar o mică parte vine din performanțele sporite ale mașinii, pentru că aici inginerii au depus cele mai mari eforturi, miniaturizând motoarele în timp ce le-au crescut puterea.
Mulți ne citesc, puțini ne susțin. Fără ajutorul tău, nu putem continua să scriem astfel de articole. Cu doar 5 euro pe lună ne poți ajuta mai mult decât crezi și poți face diferența chiar acum!
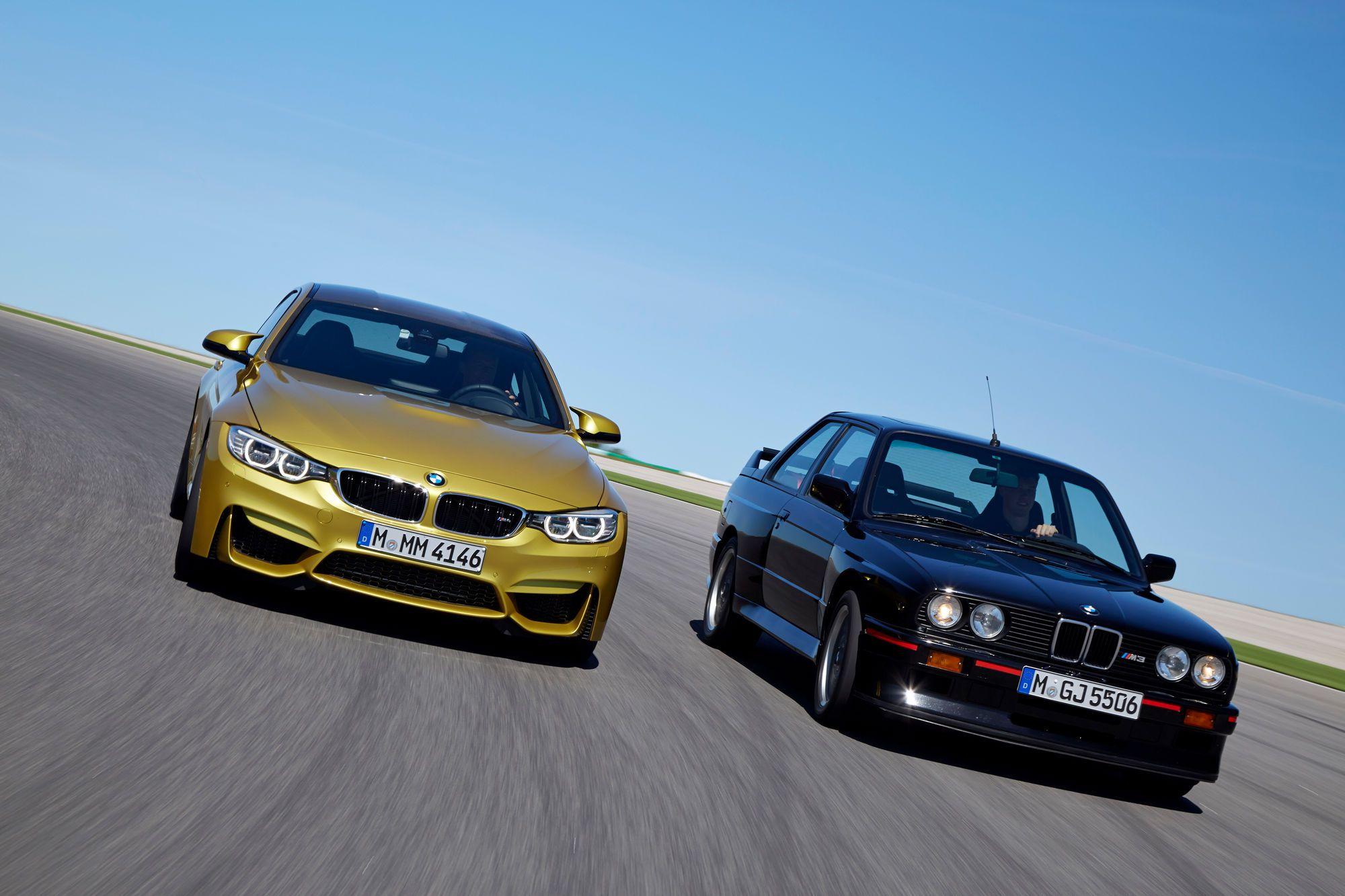
Mașinile noi sunt cu peste 300 de kilograme mai grele decât cele de dinainte de anii '90, chiar dacă sunt mai rapide, mai sigure, mai confortabile și mult mai economice
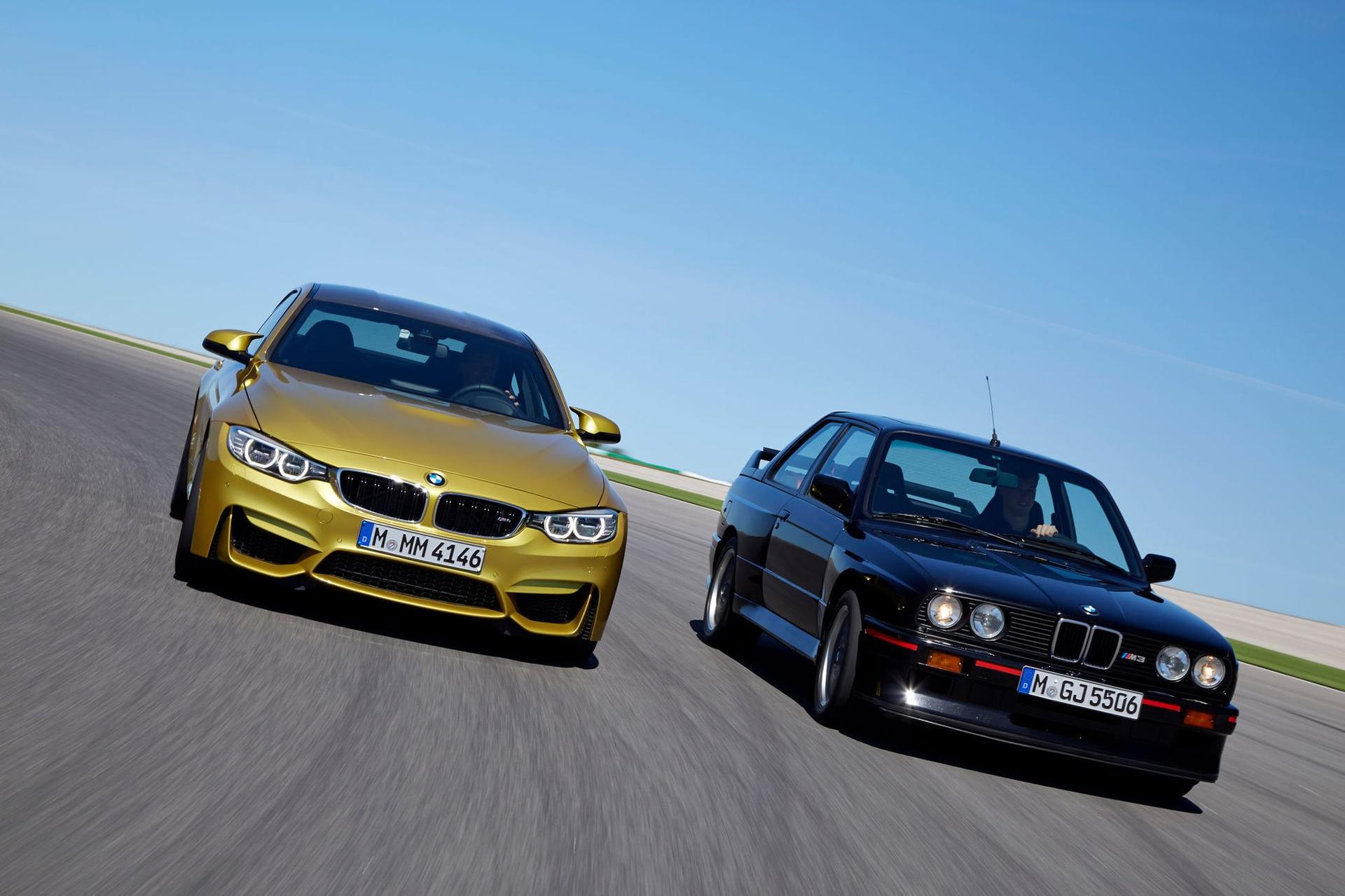
Mașinile noi sunt cu peste 300 de kilograme mai grele decât cele de dinainte de anii '90, chiar dacă sunt mai rapide, mai sigure, mai confortabile și mult mai economice
Electrificarea dublează această problemă, adăugând alte 300-350 de kilograme la greutatea totală a mașinii. Și uite așa am ajuns să vedem mașini „de familie” care trec binișor de 2 tone, în numele salvării planetei, iar asta în condițiile unei autonomii reale de circa 400 de kilometri, care nu calmează încă spaimele celor ce n-au făcut încă trecerea la electrice. Nu mai vorbesc despre epidemia de SUV-uri, care ține de alt film (de groază).
Situația asta nu mai poate continua. De undeva trebuie eliminată greutatea, pe sistemul osului de pescăruș, undeva trebuie oprită această nebunie a creșterii în greutate, pentru că altfel vom ajunge să consumăm pentru o simplă mașină de familie aproape dublul materialelor de acum 30 de ani, anulând astfel orice beneficii pentru planetă. Și, de altfel, tot procesul este nesustenabil, atât din punctul de vedere al emisiilor de CO2, cât și al resurselor materiale.
Iar aici intră în scenă printarea 3D sau producția aditivă, spuneți-i cum vreți.
Cum va salva printarea 3D lumea. Oarecum
Cel puțin 9 motive să mergi la IQ DIGITAL SUMMIT - Cluj-Napoca – 14 IUNIE (P)
Unii dintre cei mai mari lideri de tehnologie vin la Cluj-Napoca pe 14 iunie, iar cititorii PressOne pot avea acces gratuit pentru a-i vedea și asculta.
Producția de cipuri: între ambițiile UE și realitatea din teren
UE nici măcar nu se apropie de atingerea obiectivelor prevăzute în legea privind cipurile, adoptată în 2023, iar cel mai recent raport al Curții de Conturi Europene trage un semnal de alarmă.
Glumesc, evident că producția aditivă nu va salva planeta prin forțe proprii, ci e doar una dintre multele piese de puzzle necesare unei lumi în care să eliminăm risipa și să putem refolosi aproape la nesfârșit aceleași resurse.
Fără a intra în detalii tehnice prea mari, o piesă printată 3D poate economisi peste 40% din greutatea unei piese similare pe care o înlocuiește. Unde am mai văzut acest procent? Păi exact mai sus. Asta înseamnă, într-o lume ideală, că am putea reduce greutatea mașinilor actuale cu 30-50% dacă le-am face cap-coadă la imprimante 3D.
O piesă printată 3D poate fi cu 50% mai ușoară decât una clasică.
Și arată ca și când ar fi fost făcută de natură, nu de un inginer.
Deși e rodul muncii unei întregi echipe de ingineri.
Un newsletter pentru cititori curioși și inteligenți.
Sunt curios
Lucru care nu se va întâmpla prea curând, îmi spune inginerul BMW care-mi face turul campusului de producție aditivă din Oberschleißheim, un orășel cu nume imposibil de pronunțat, aflat la nord de Munchen. Roțile, de exemplu, nu vor putea fi făcute așa, decât dacă încep să arate precum cele dezvoltate de Michelin. Parbrizul, niciodată.
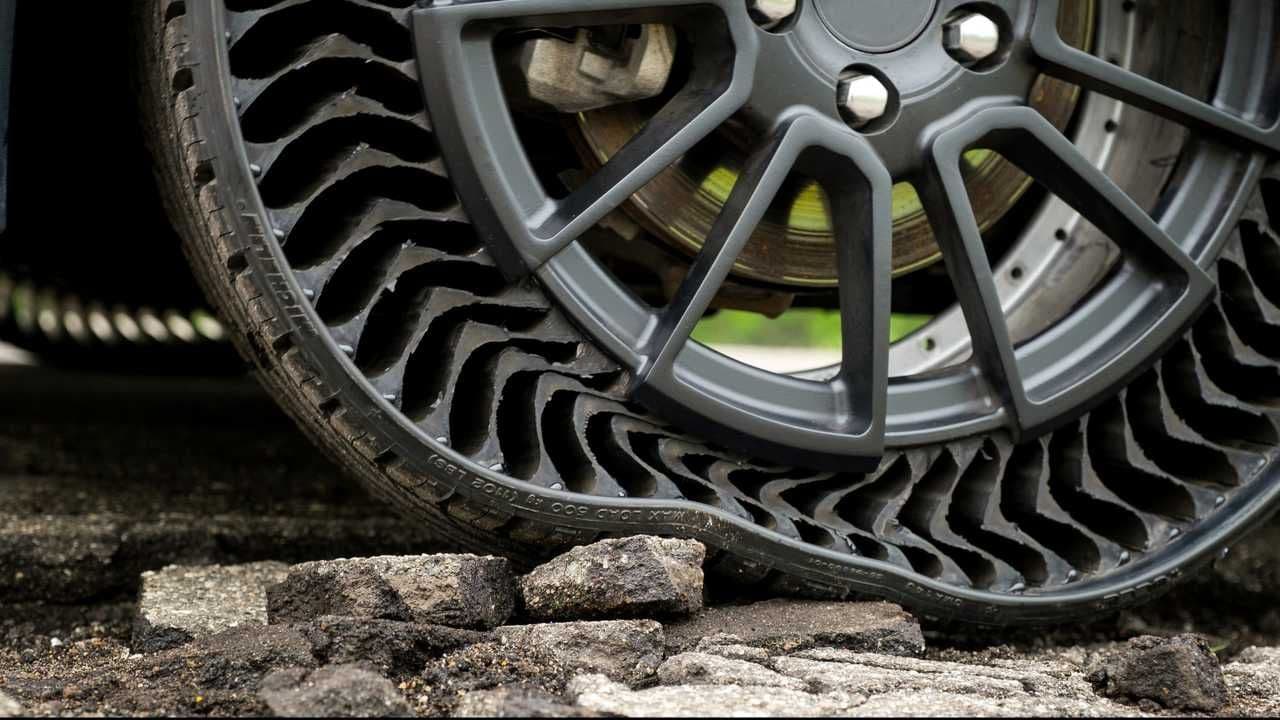
La un moment dat, poate că roțile mașinilor vor fi printate 3D. Deocamdată e posibil, dar total nepractic
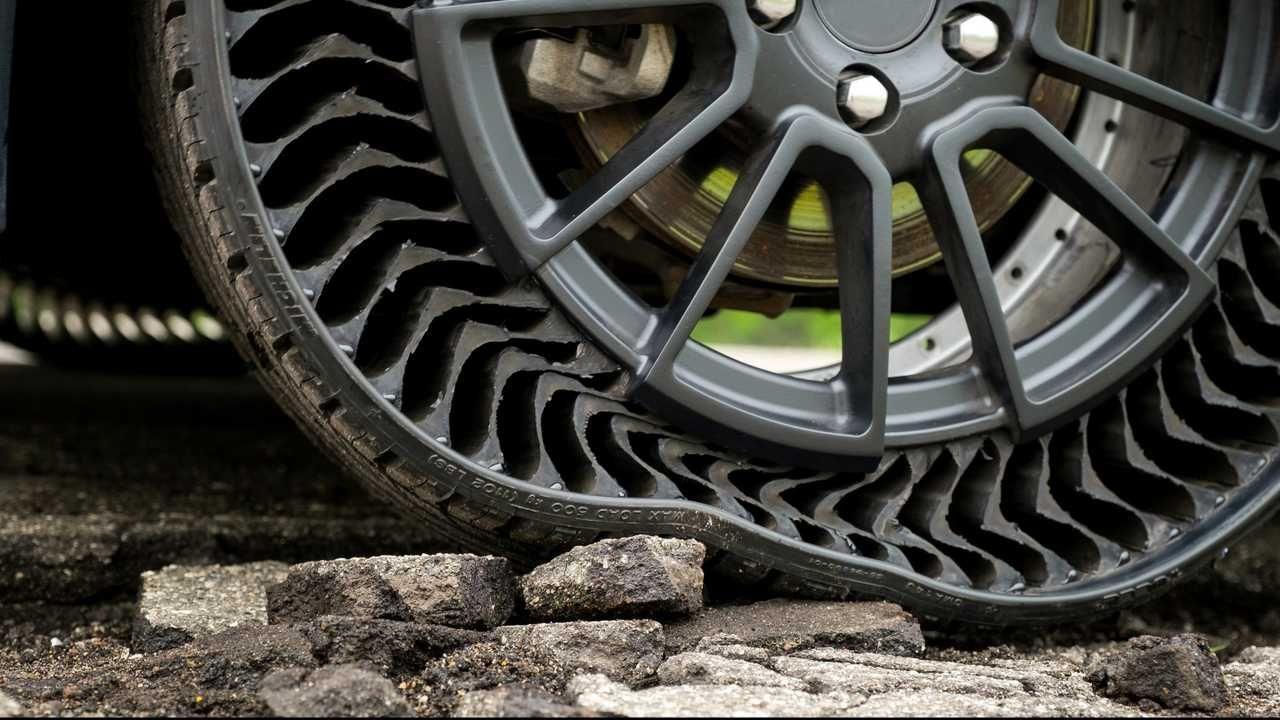
La un moment dat, poate că roțile mașinilor vor fi printate 3D. Deocamdată e posibil, dar total nepractic
Apoi, o mașină e de fapt un puzzle tridimensional făcut din 20-30.000 de piese componente, dintre care o mare parte, în special cele simple, nu au de ce să fie tipărite tridimensional.
Procedeul de printare 3D face diferența exact la piesele complexe. O balama sau un suport de prindere la 90 de grade folosesc mult material atunci când sunt produse prin ștanțare. Regândite de inginerii din campusul de producție aditivă, ele arată deja ca niște articulații de pescăruș, fiind în același timp mult mai ușoare, dar și mai rezistente decât piesele inițiale.
De fapt, mai toate piesele create prin acest procedeu arată ca și când ar fi fost dezvoltate de natură, nu de om. De ce? Pentru că se inspiră tocmai din natură - au forme fluide, orientate în mod specific pentru a-și împlini funcția cu consum cât mai mic de materiale.
În plus, pentru că folosesc pulberi de metal sau de polimeri, permit substituirea materialelor clasice cu noi materiale, unele dintre ele biodegradabile - inclusiv elastomeri fabricați din deșeurile din lemn. Risipa este practic eliminată - inginerul german îmi arată cum toate bucățile rămase în urma procesului de printare 3D sunt reciclate în cadrul aceluiași flux tehnologic.
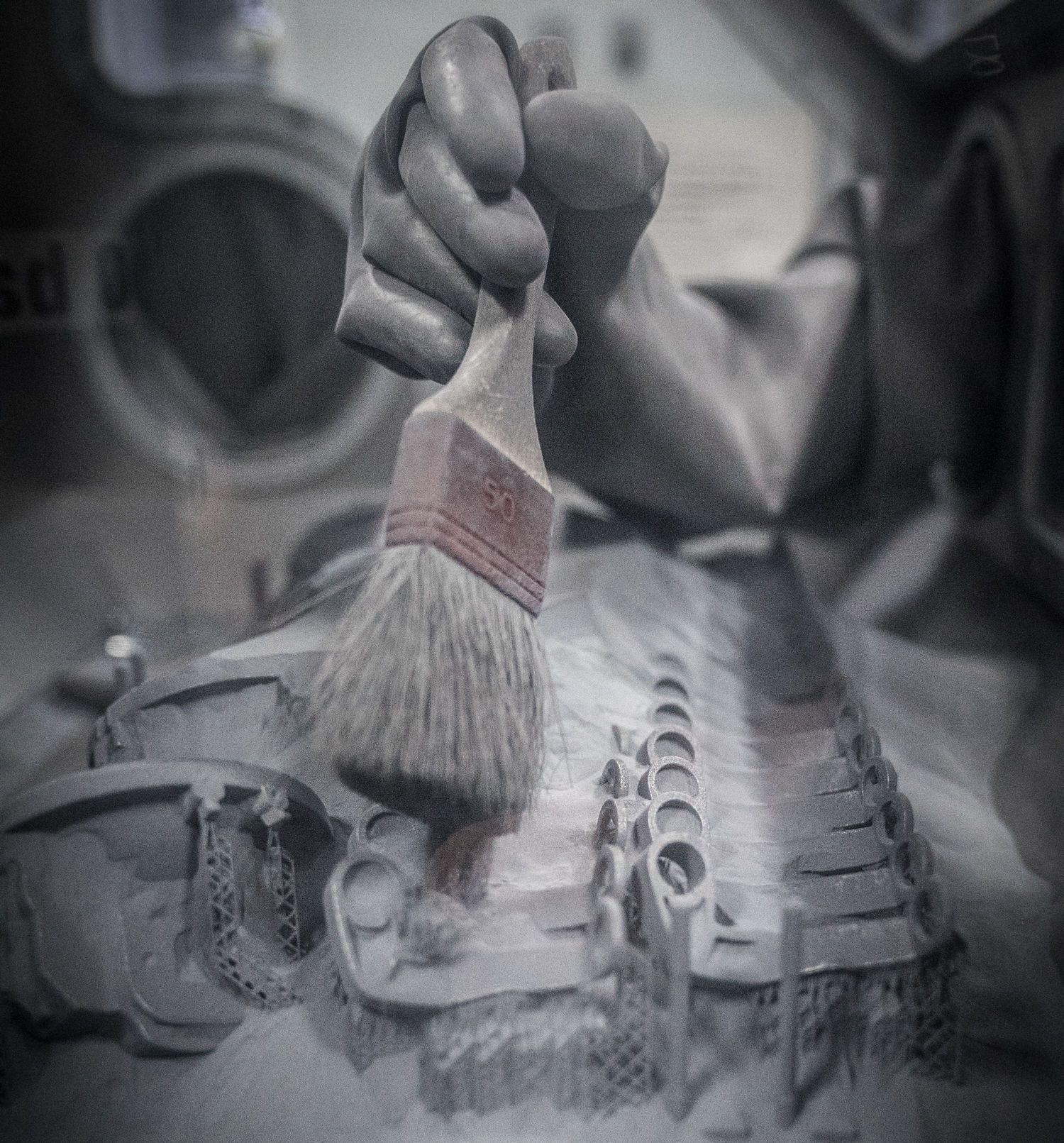
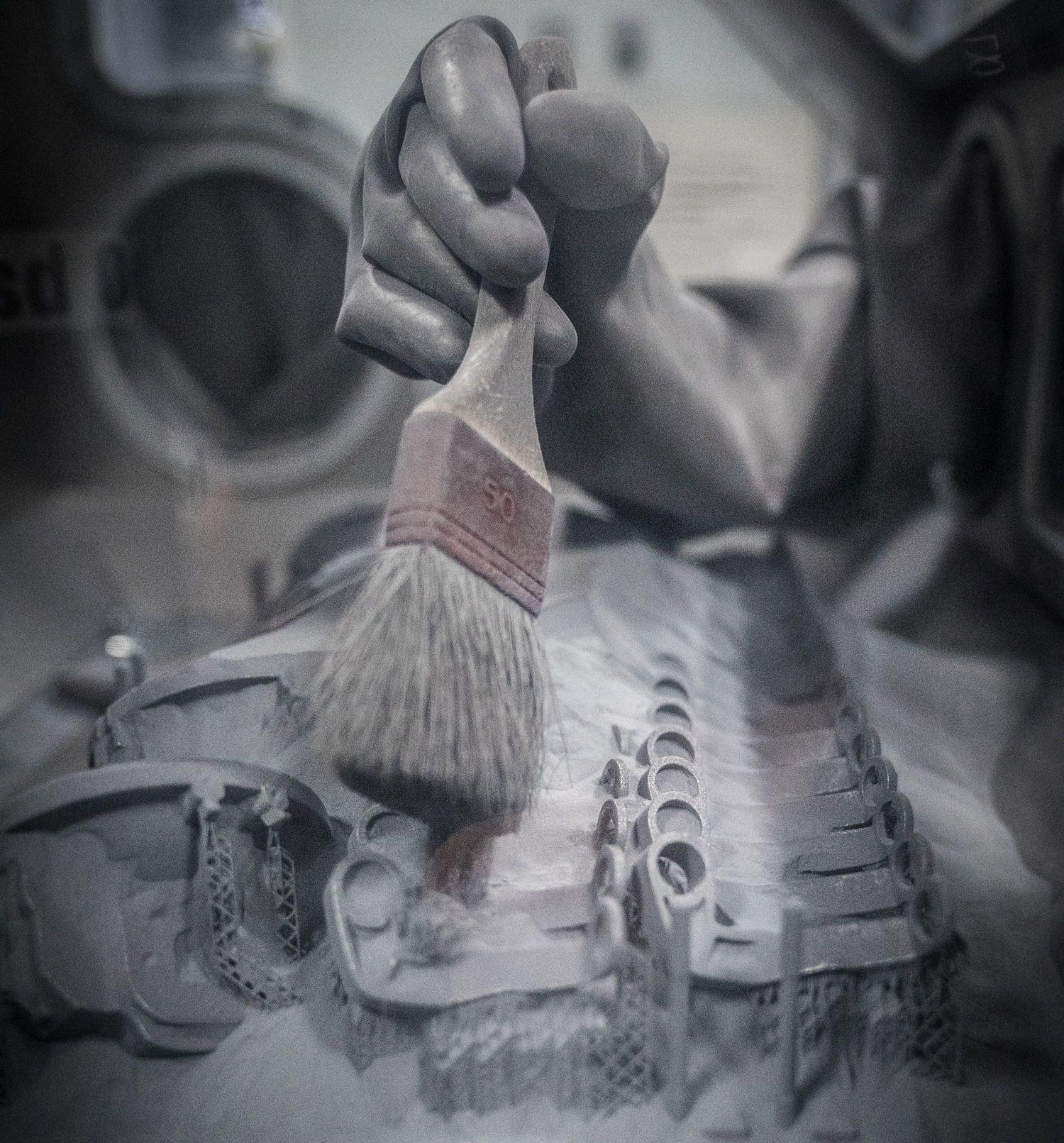
Treptat se va ajunge ca o parte tot mai mare din mașină să fie fabricată așa, inclusiv piese grele, care țin de transmisie și trenul de rulare. Deocamdată, suntem abia la a doua treaptă dintr-o scară destul de înaltă și de lungă. Cea în care se trece treptat de la producția de prototipuri și piese unicat prin acest procedeu, cu costuri mult mai mici, la producția de serie mică sau medie de piese de schimb sau chiar de subansambluri de serie mare.
Magie cu lasere și pulberi
Magia se întâmplă în niște mașinării echipate cu lasere, care sunt alimentate cu pulberi din metal sau polimeri, în funcție de tipul de producție dorit. E ca și când ai vedea o imprimantă la lucru, numai că aceasta adaugă strat după strat de pulbere, iar laserele topesc ultrarapid exact acele zone necesare pentru crearea piesei dorite, tot strat după strat. Apoi piesa astfel rezultată este separată de restul matriței și trimisă la finisat.
Resturile matriței sunt recuperate și transformate din nou în pulbere, pentru că, nefiind afectate de procesul de topire, se fac literalmente praf printr-o simplă presiune. Toate imensele imprimante din campus sunt alimentate cu energie electrică, astfel încât atmosfera este complet diferită de cea a unei prese auto tipice, unde se zguduie podeaua sub picioarele tale. De afară nici n-ai ști că aici se produc piese auto extrem de complexe.
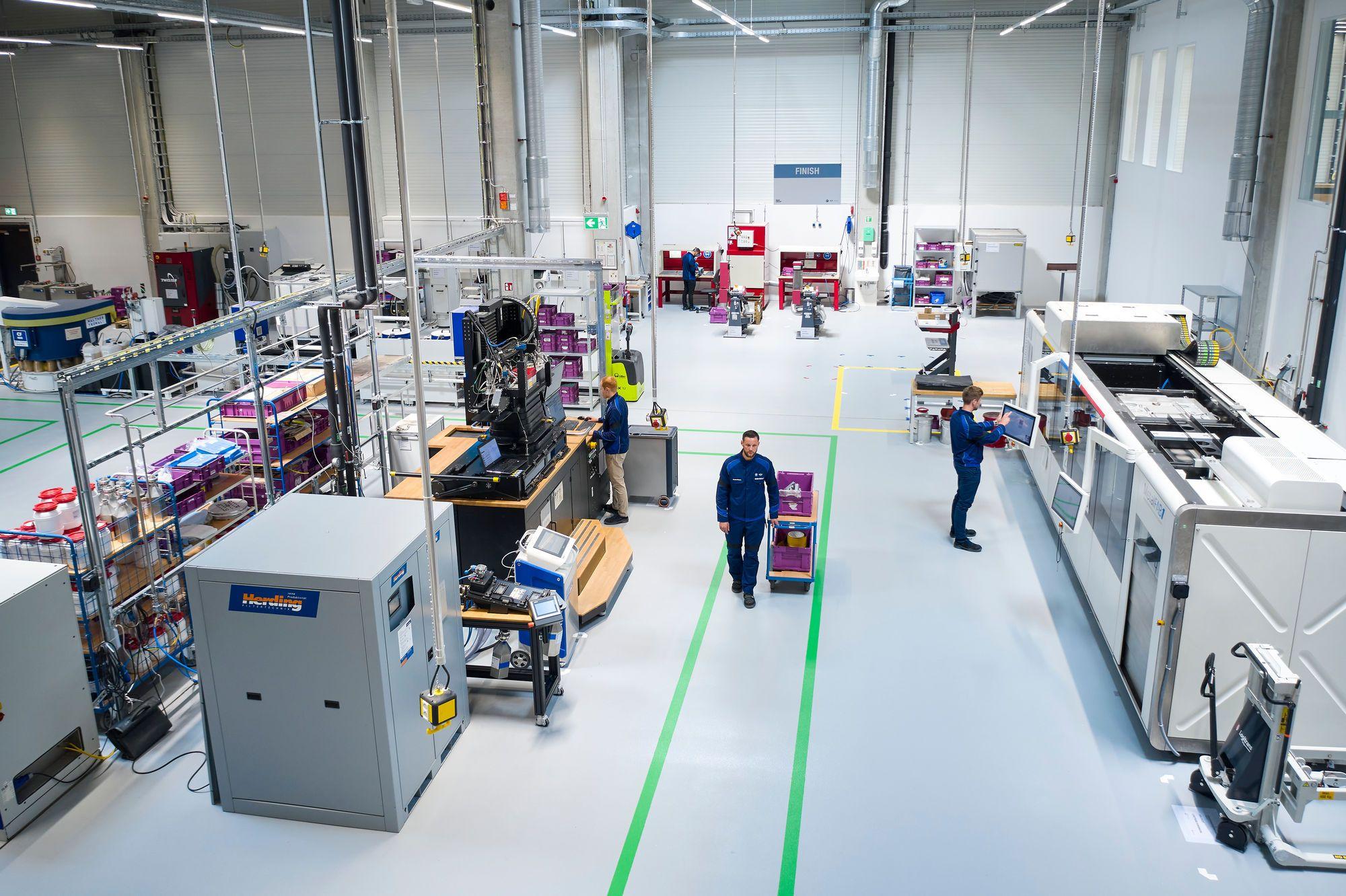
Ca un fel de farmacie. Așa arată uzinele viitorului, deja de pe acum
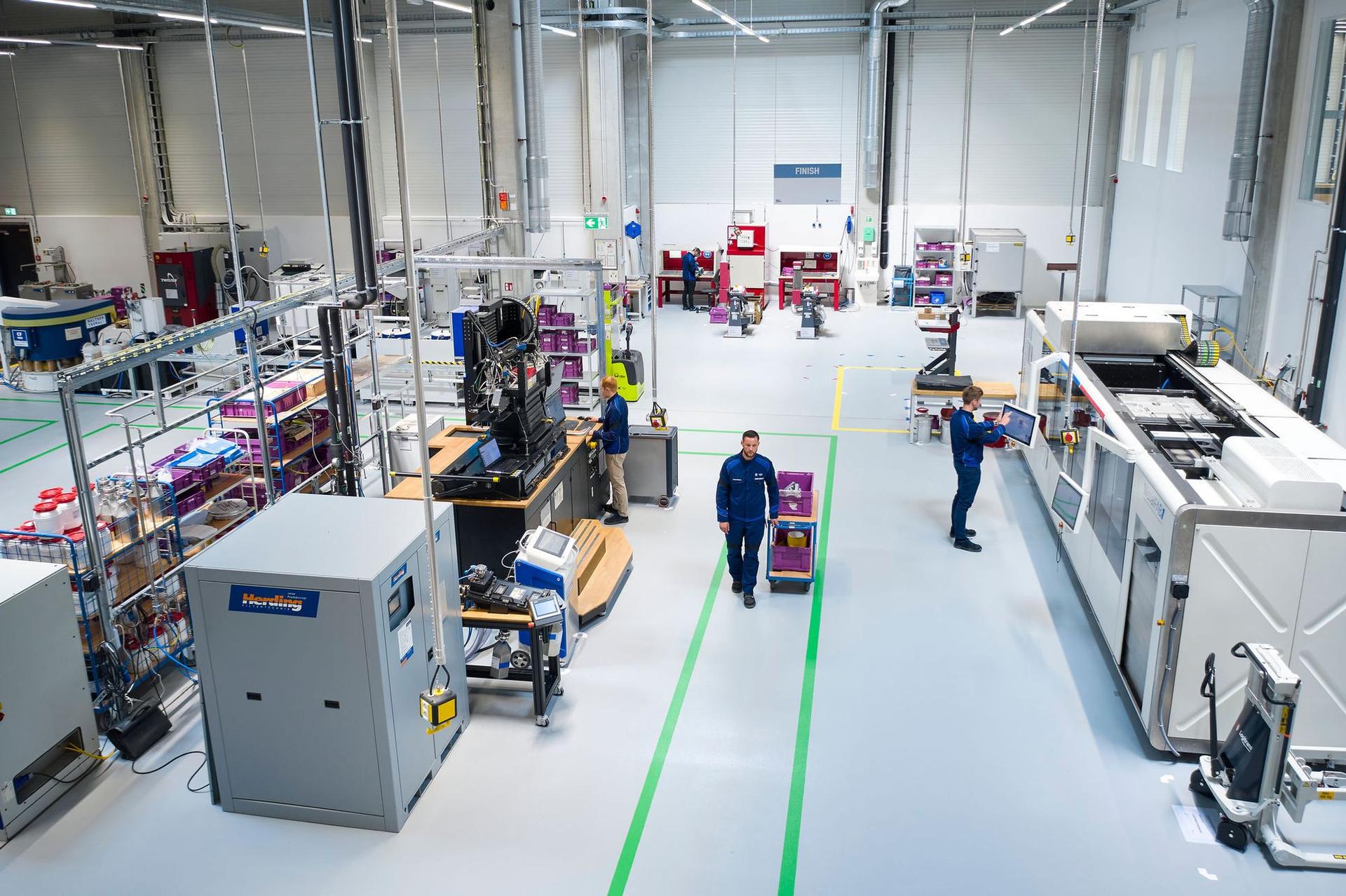
Ca un fel de farmacie. Așa arată uzinele viitorului, deja de pe acum
Cele 50 de sisteme industriale de printare 3D din campusul AM de lângă Munchen produc circa 50.000 de componente pe an, precum și peste 10.000 de subansambluri individuale și noi, folosind tehnologia Laser Powder Bed Fusion (LPBF), prin care pudra de metal e topită cu ajutorul laserelor. Procedeul economisește, în acest campus, circa 50% din greutatea pieselor respective. Se economisesc și bani: între 30% pentru prototipuri și 50% pentru piesele de serie.
De altfel, cea mai mare parte a producției este automatizată, roboții ocupându-se de aproape tot. Module complet automatizate transportă pulberea către stațiile de lucru, acolo unde materialele sunt pregătite în mod independent. Inclusiv post-procesarea pieselor rezultate este făcută la stații de lucru automate, doar anumite procese de finisare și control fiind lăsate pe seama oamenilor. Peste toate veghează o inteligență artificială care corelează datele colectate de la toate procesele de producție cu cele legate de calitatea pieselor rezultate. Cum e ceva în neregulă, cum se iau și măsurile necesare.
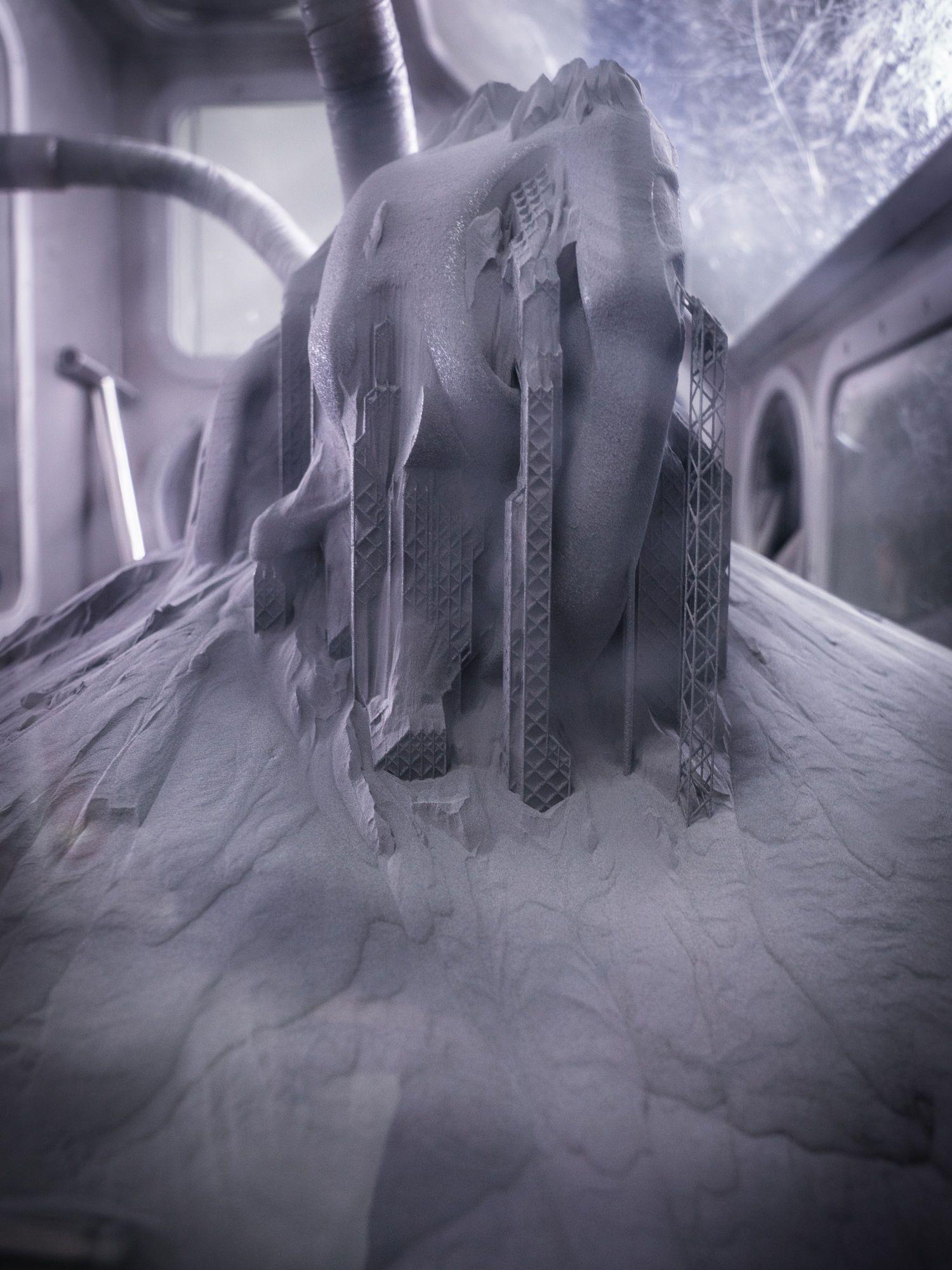
Pare a fi o inimă creată într-un laborator dintr-un film SF. În realitate, e un etrier dedicat unui model super sport
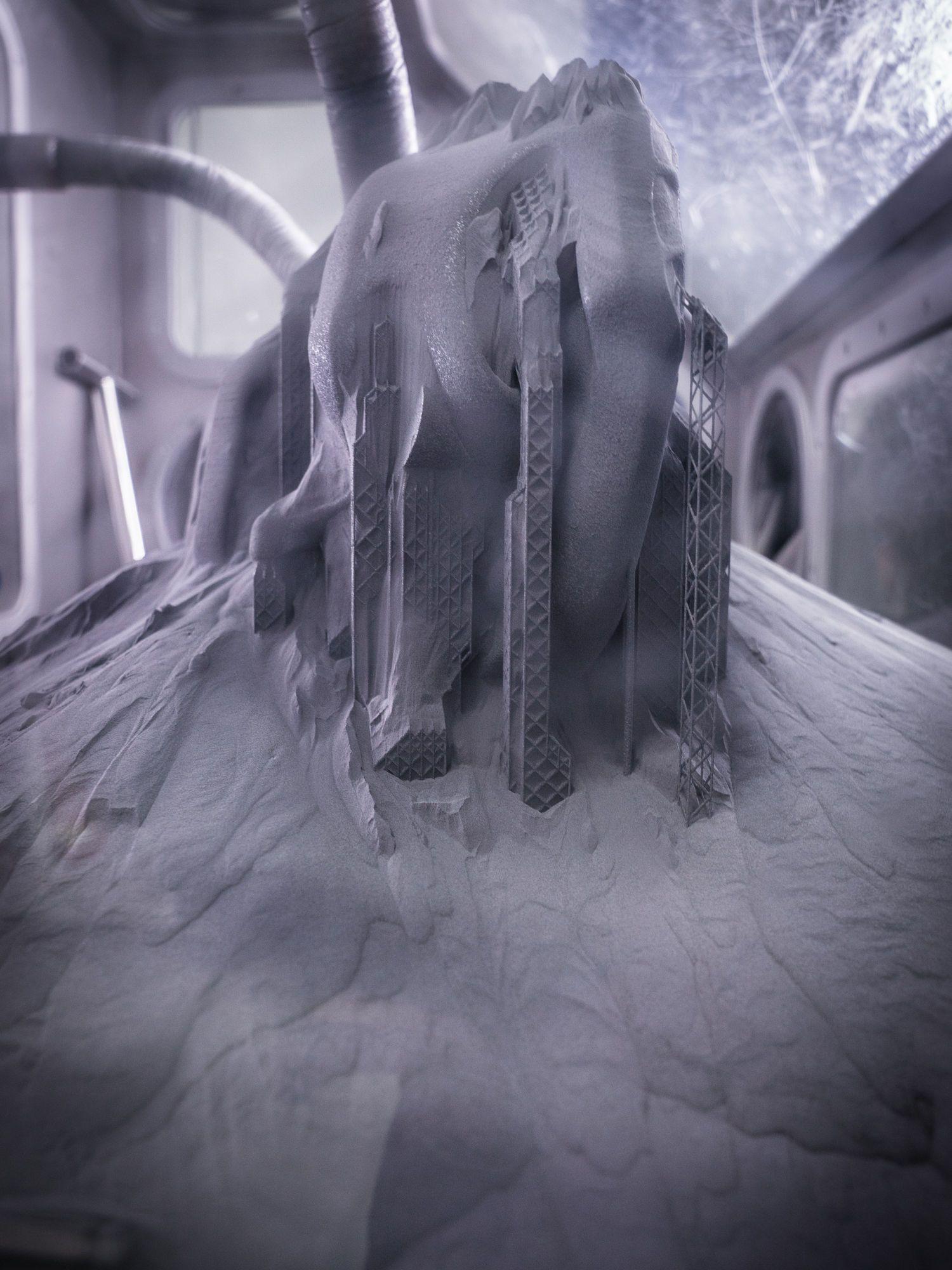
Pare a fi o inimă creată într-un laborator dintr-un film SF. În realitate, e un etrier dedicat unui model super sport
Procesul de producție aditivată nu doar că permite subansambluri mai ușoare și mai rezistente, dar permite și crearea unor piese care ar fi fost imposibil de realizat prin procedeele clasice. De aici pleacă piese unice dedicate clienților de Rolls-Royce, cât și sute de piese unice destinate personalizării mașinilor BMW. În anumite cazuri, piesele proiectate de inginerii de aici ajung să fie fabricate în serii mai mari - cum ar fi cazul cheilor personalizate pentru mașinile MINI.
Ce ne rezervă viitorul
Dacă în campusul de lângă Munchen am văzut cum imprimantele creează piese 3D din pulberi de polimeri sau metal, producția de piese mai complexe, din materiale compozite, va fi făcută printr-un proces diferit, numit binder jet additive manufacturing, în traducere - producție aditivă cu jet de liant.
Una dintre problemele printării 3D prin pulberi este scalarea - creșterea debitului de piese realizate. Pe scurt, numărul laserelor folosite de fiecare imprimantă pentru printarea 3D se va tripla în curând, iar spre finalul deceniului inginerii se așteaptă ca această tehnologie să aibă un debit de peste 10 de ori mai mare decât acum. Efectul? Serii mai mari de piese, produse mai rapid, care vor sări de milionul de bucăți per subansamblu.
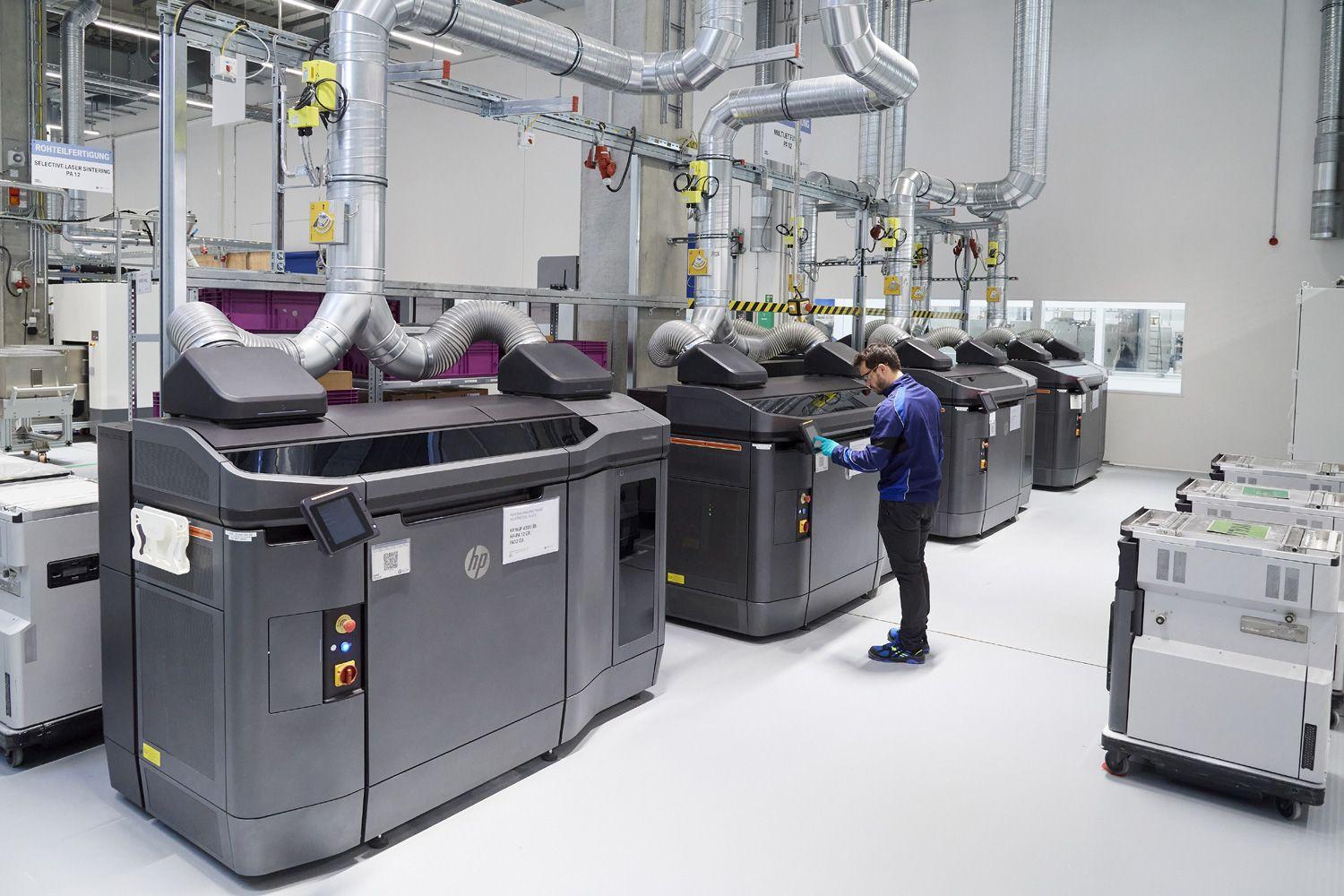
Tot imprimante HP, ca aceea pe care o ai pe birou, numai că acestea printează cu polimeri piese de serie mică sau chiar pentru prototipuri
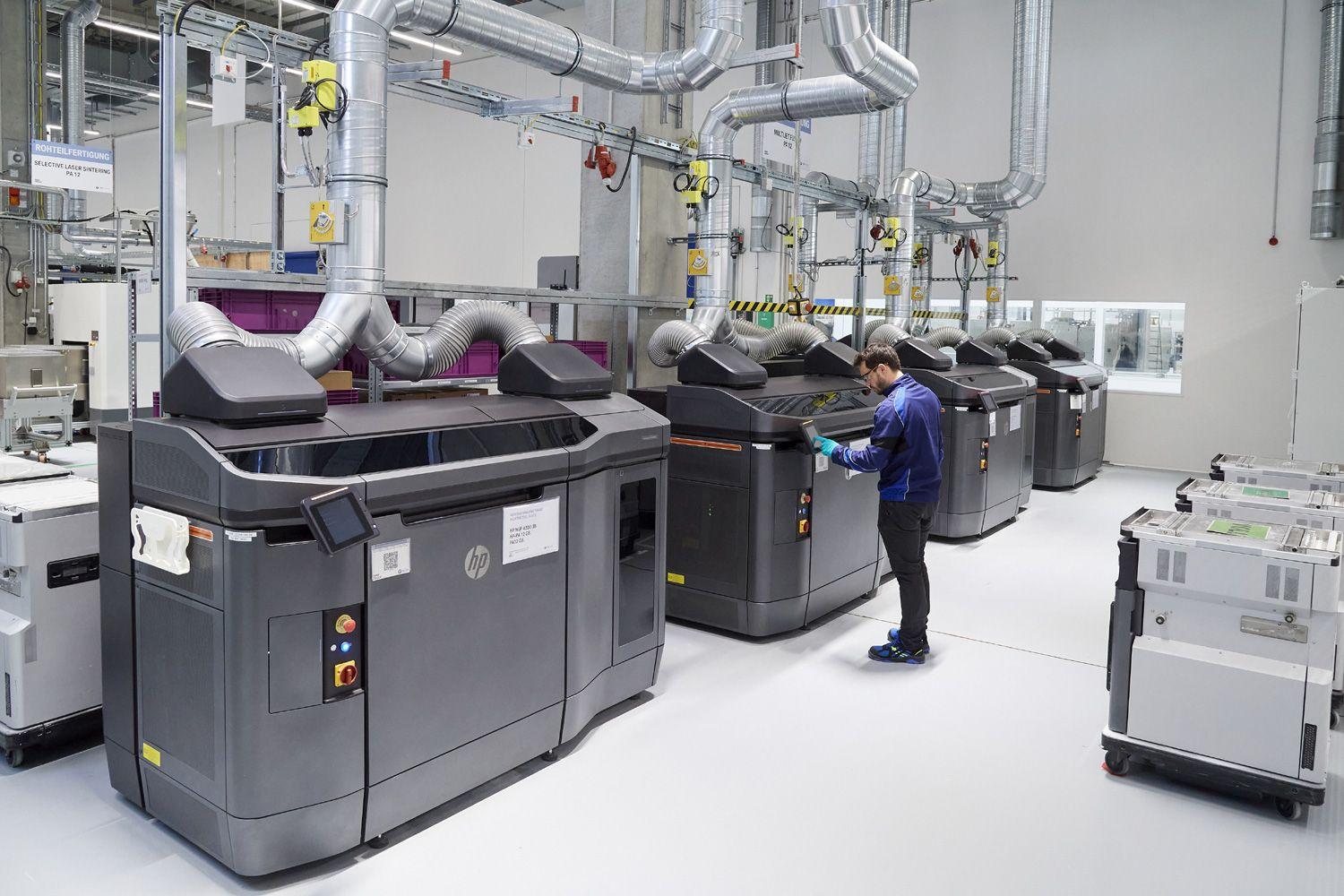
Tot imprimante HP, ca aceea pe care o ai pe birou, numai că acestea printează cu polimeri piese de serie mică sau chiar pentru prototipuri
Dar debitul și mai ales mărimea și complexitatea pieselor printate 3D vor crește în special prin procedee noi de producție precum aditivarea cu jet de liant. Fără a intra în detalii tehnice complicate, acestea permit folosirea de pulberi mult mai ieftine, într-un proces care este mult mai ușor scalabil la nivelul unor producții de serie destinate mașinilor accesibile, iar nu doar celor premium sau de lux.
Se duce o luptă între giganții auto pentru a fi primii care stăpânesc cu adevărat toate aceste tehnologii noi, pentru că de ele depinde însuși viitorul lor. În joc sunt implicate și aceleași companii care produc banalele imprimante de pe biroul nostru - HP este unul dintre liderii imprimantelor cu polimeri, de exemplu, pe care le-am văzut la lucru chiar lângă Munchen.
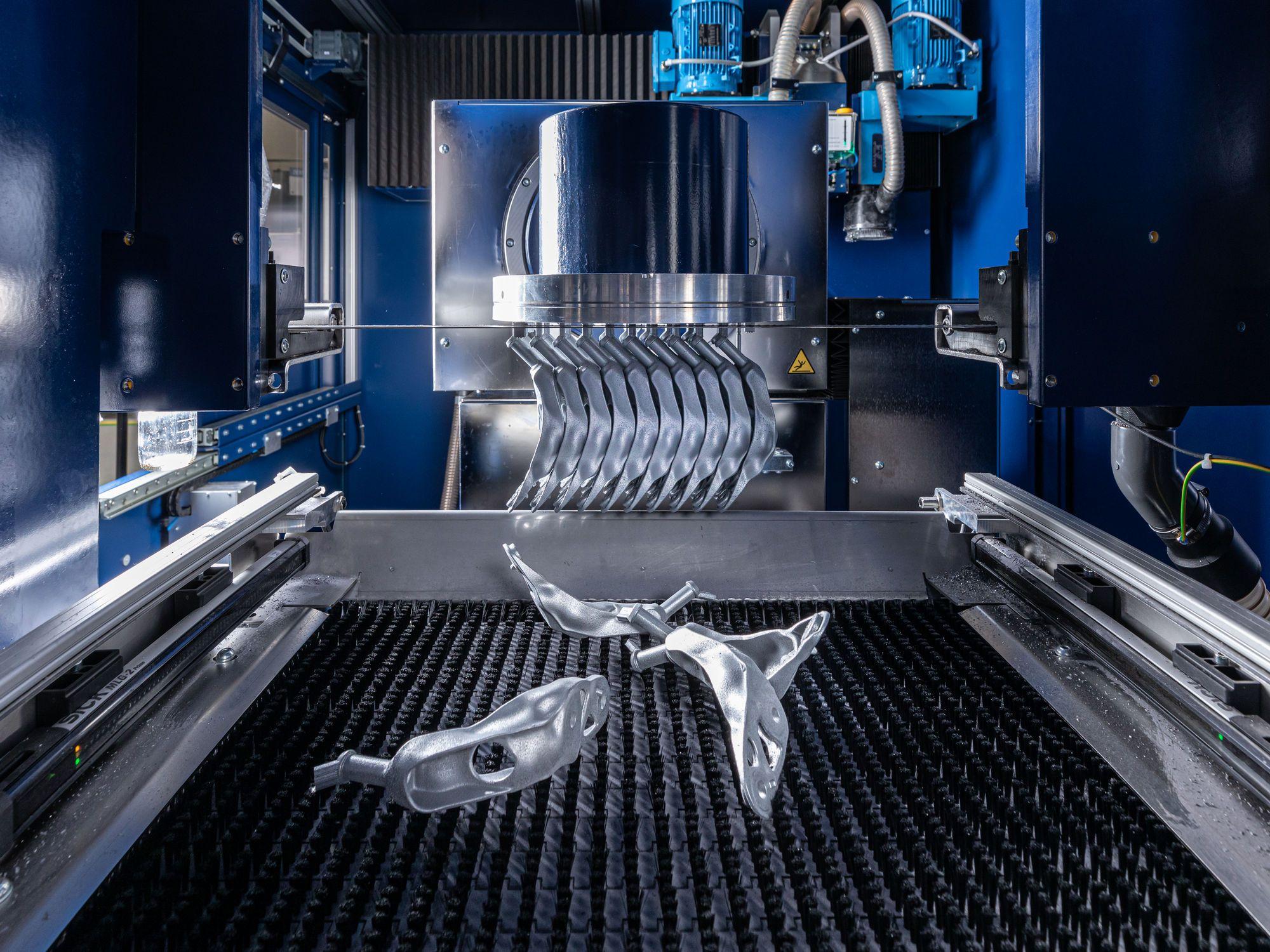
În mai puțin de zece ani, destule dintre piesele unei mașini vor fi produse în acest mod. Dar mai avem un drum foarte lung de parcurs până la a ajunge la un procent important
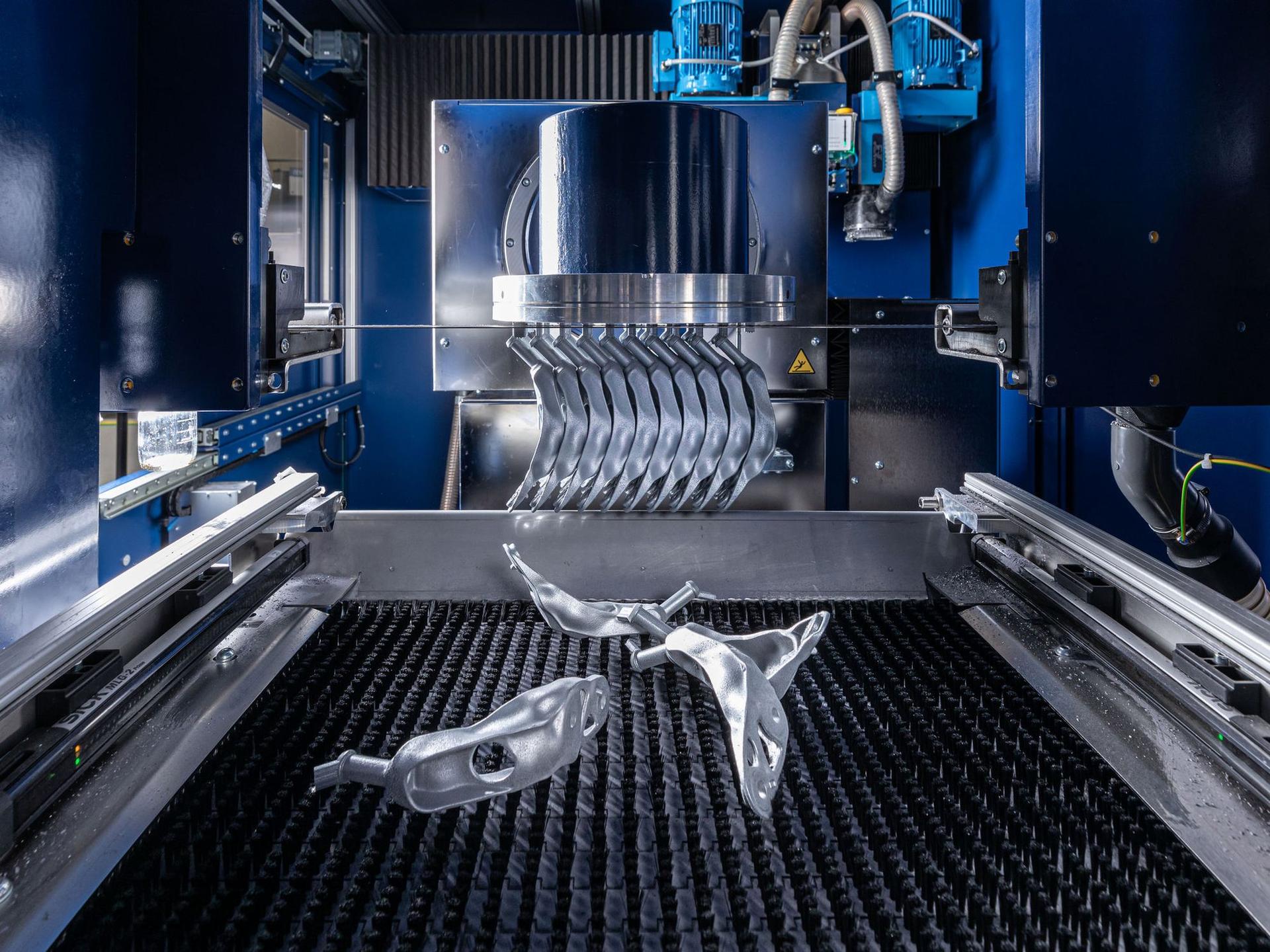
În mai puțin de zece ani, destule dintre piesele unei mașini vor fi produse în acest mod. Dar mai avem un drum foarte lung de parcurs până la a ajunge la un procent important
Evident, nu doar mașinile sunt vizate. Industria aeronautică, industria farmaceutică și cea medicală sunt doar câteva dintre zonele care vor beneficia din plin de imprimarea tridimensională. Ca să nu mai zic de industria ciocolatei, acolo unde bucătarii fac deja minuni cu astfel de imprimante, dar deja îmi pare rău că am adus vorba despre asta.
Pe măsură ce aceste procedee se vor extinde în cadrul industriei auto, vom avea mașini ale căror structuri vor semăna din ce în ce mai mult cu cele organice - cel puțin în privința scheletului și al pieselor complexe.
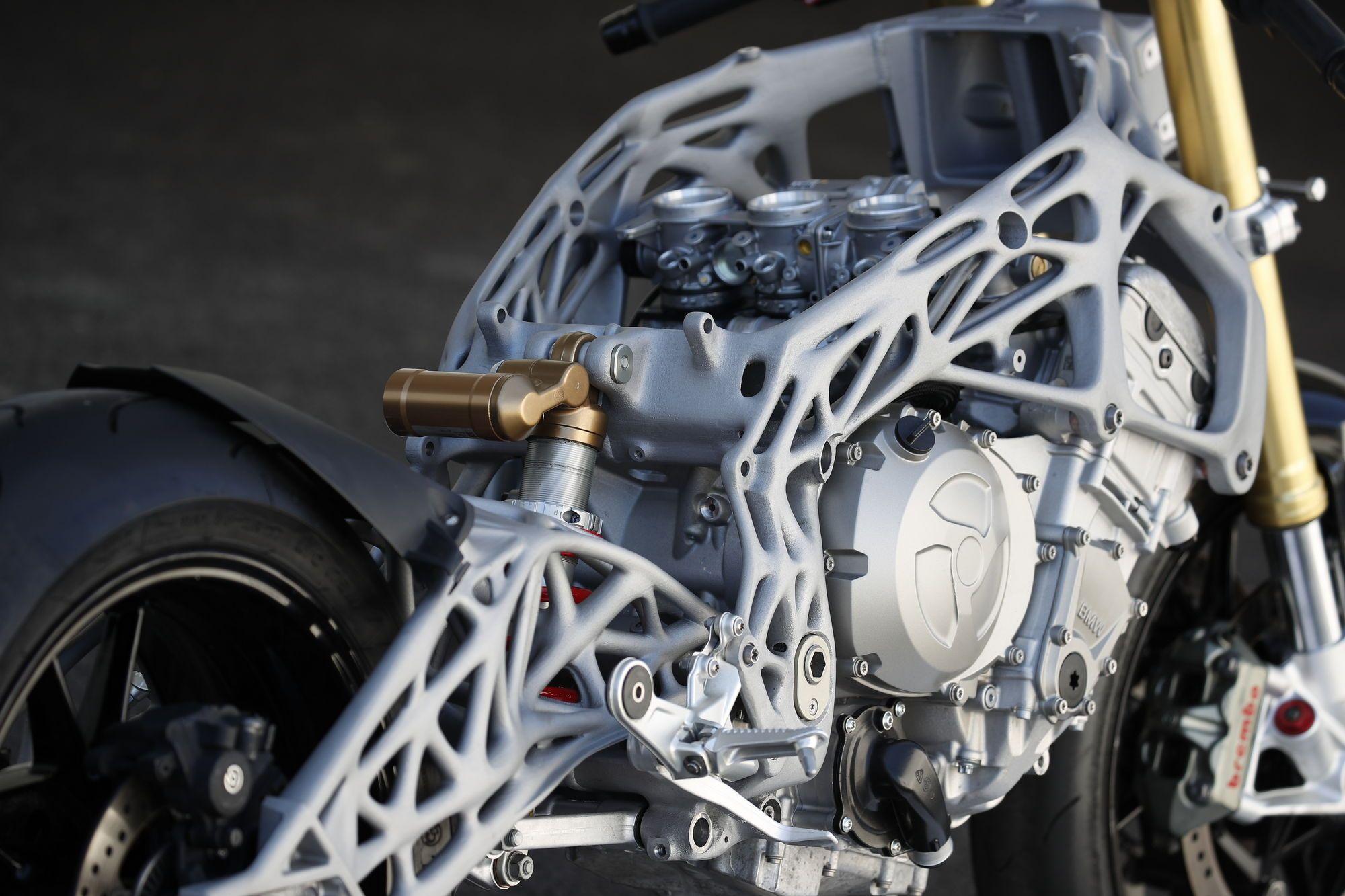
Nu doar mașinile, ci și motocicletele vor putea fi construite cu piese printate 3D în viitor. Deocamdată vorbim de prototipuri și serii unicat sau mici
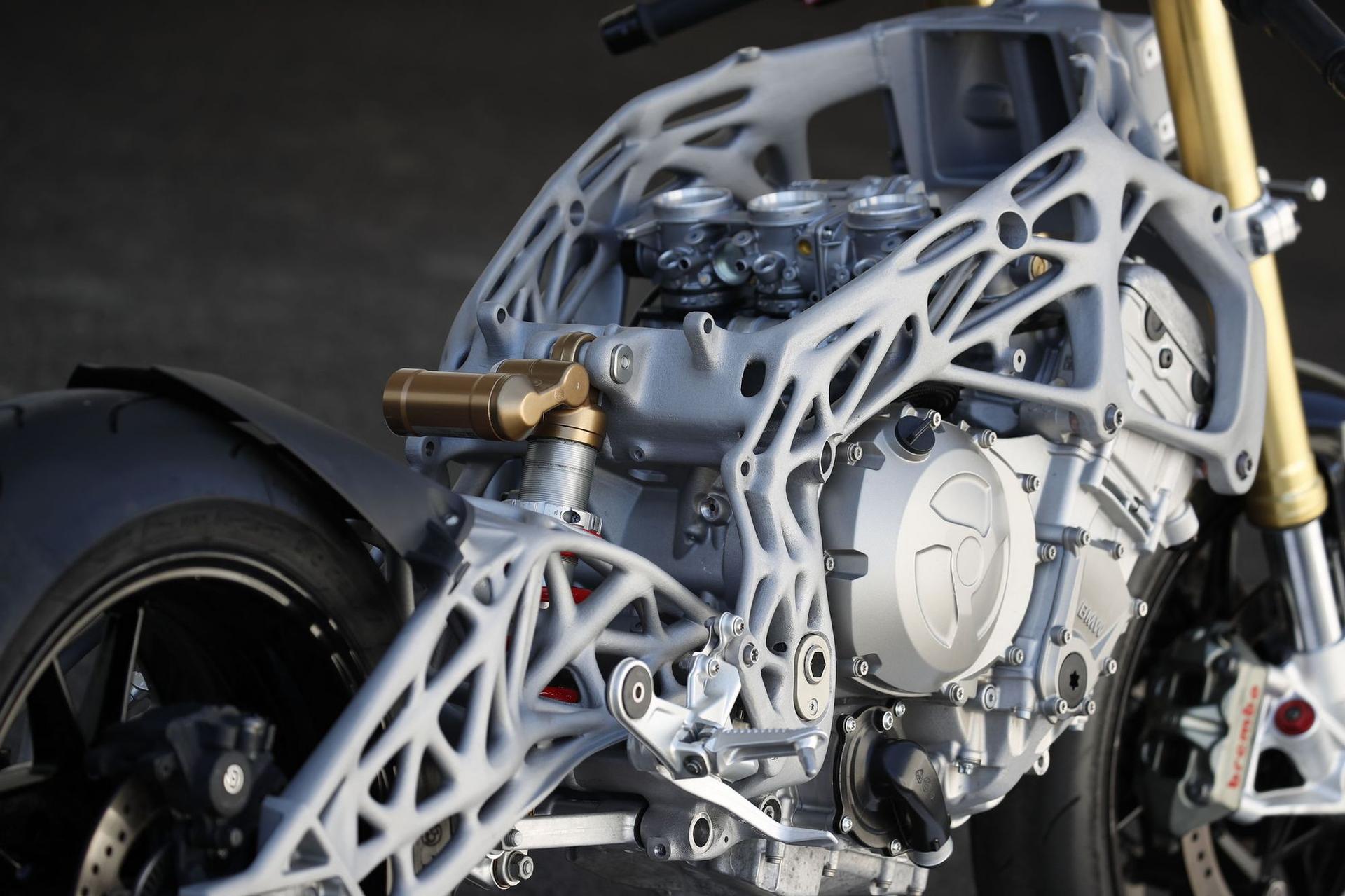
Nu doar mașinile, ci și motocicletele vor putea fi construite cu piese printate 3D în viitor. Deocamdată vorbim de prototipuri și serii unicat sau mici
Am putea visa la o perioadă în care o mașină electrică cu 4-500 de kilometri autonomie va ajunge să fie la fel de „ușoară” precum una cu motor pe combustie, dar mai avem de așteptat până atunci.
Am tot vorbit despre roboți și procese automate. De fapt, tot ce am descris mai sus este rezultatul muncii a mii de ingineri și a peste trei decenii de experimente. Azi, ei proiectează deja tehnologiile care ne vor duce, treptat, acolo. Este, de altfel, singura cale prin care vom putea repara tot ce am făcut greșit până acum.
Totul este să învățăm de la natură.
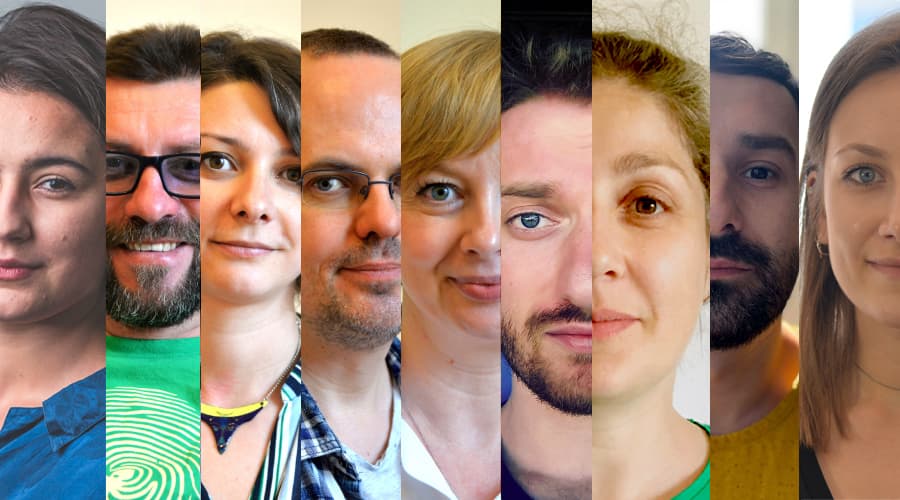
Avem nevoie de ajutorul tău!
Mulți ne citesc, puțini ne susțin. Asta e realitatea. Dar jurnalismul independent și de serviciu public nu se face cu aer, nici cu încurajări, și mai ales nici cu bani de la partide, politicieni sau industriile care creează dependență. Se face, în primul rând, cu bani de la cititori, adică de cei care sunt informați corect, cu mari eforturi, de puținii jurnaliști corecți care au mai rămas în România.
De aceea, este vital pentru noi să fim susținuți de cititorii noștri.
Dacă ne susții cu o sumă mică pe lună sau prin redirecționarea a 3.5% din impozitul tău pe venit, noi vom putea să-ți oferim în continuare jurnalism independent, onest, care merge în profunzime, să ne continuăm lupta contra corupției, plagiatelor, dezinformării, poluării, să facem reportaje imersive despre România reală și să scriem despre oamenii care o transformă în bine. Să dăm zgomotul la o parte și să-ți arătăm ce merită cu adevărat știut din ce se întâmplă în jur.
Ne poți ajuta chiar acum. Orice sumă contează, dar faptul că devii și rămâi abonat PressOne face toată diferența. Poți folosi direct caseta de mai jos sau accesa pagina Susține pentru alte modalități în care ne poți sprijini.
Vrei să ne ajuți? Orice sumă contează.
Share this